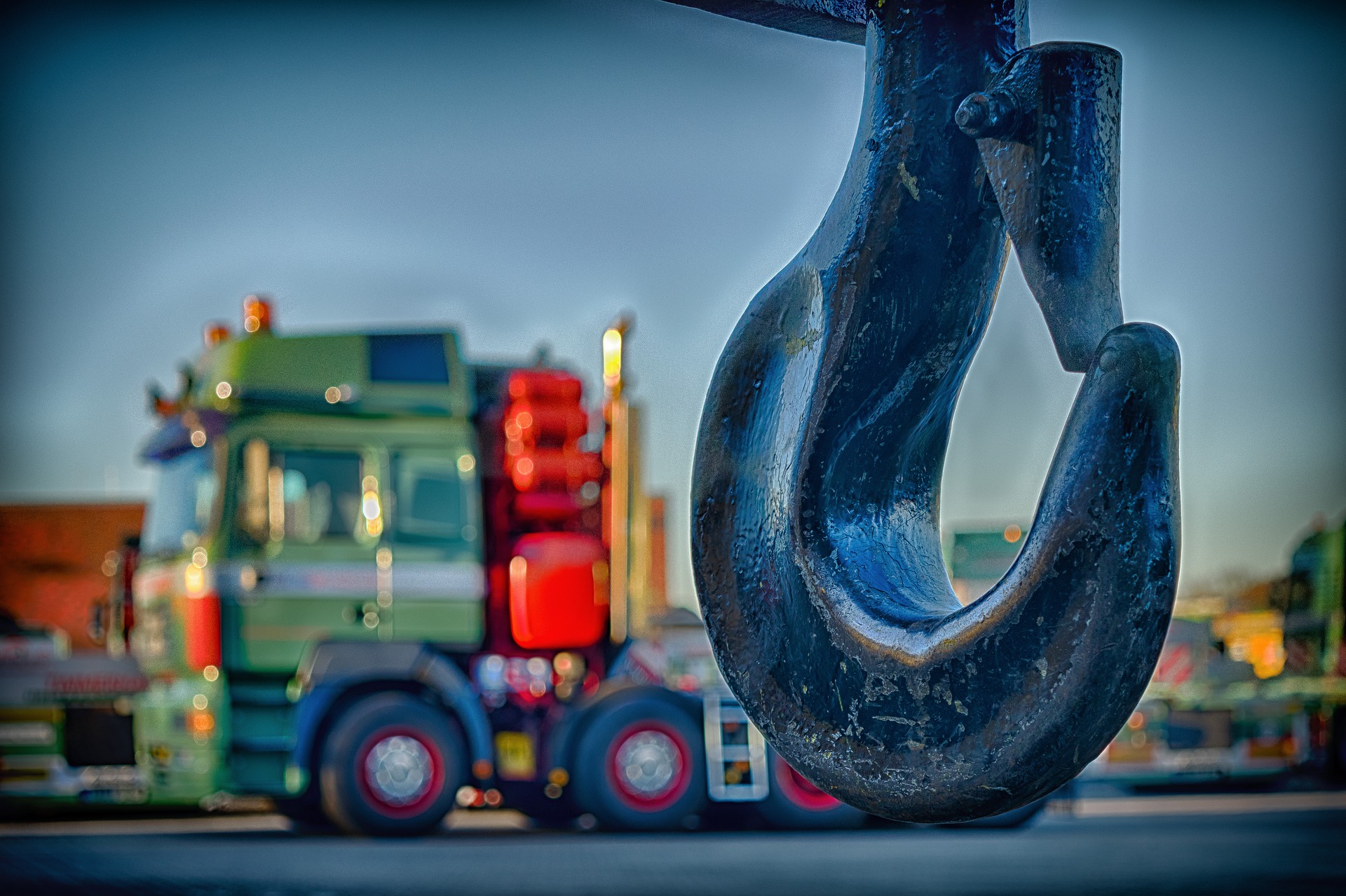
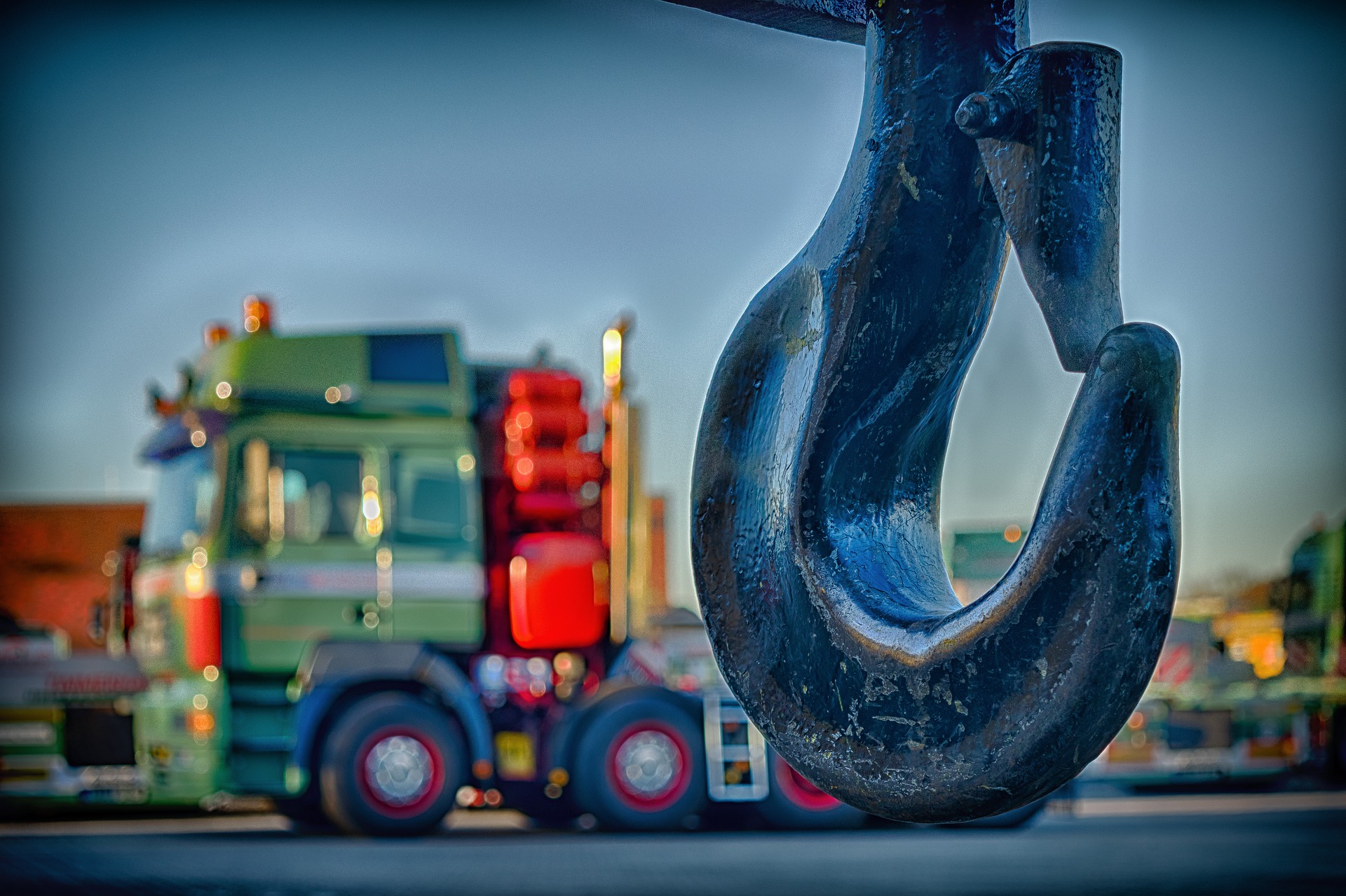
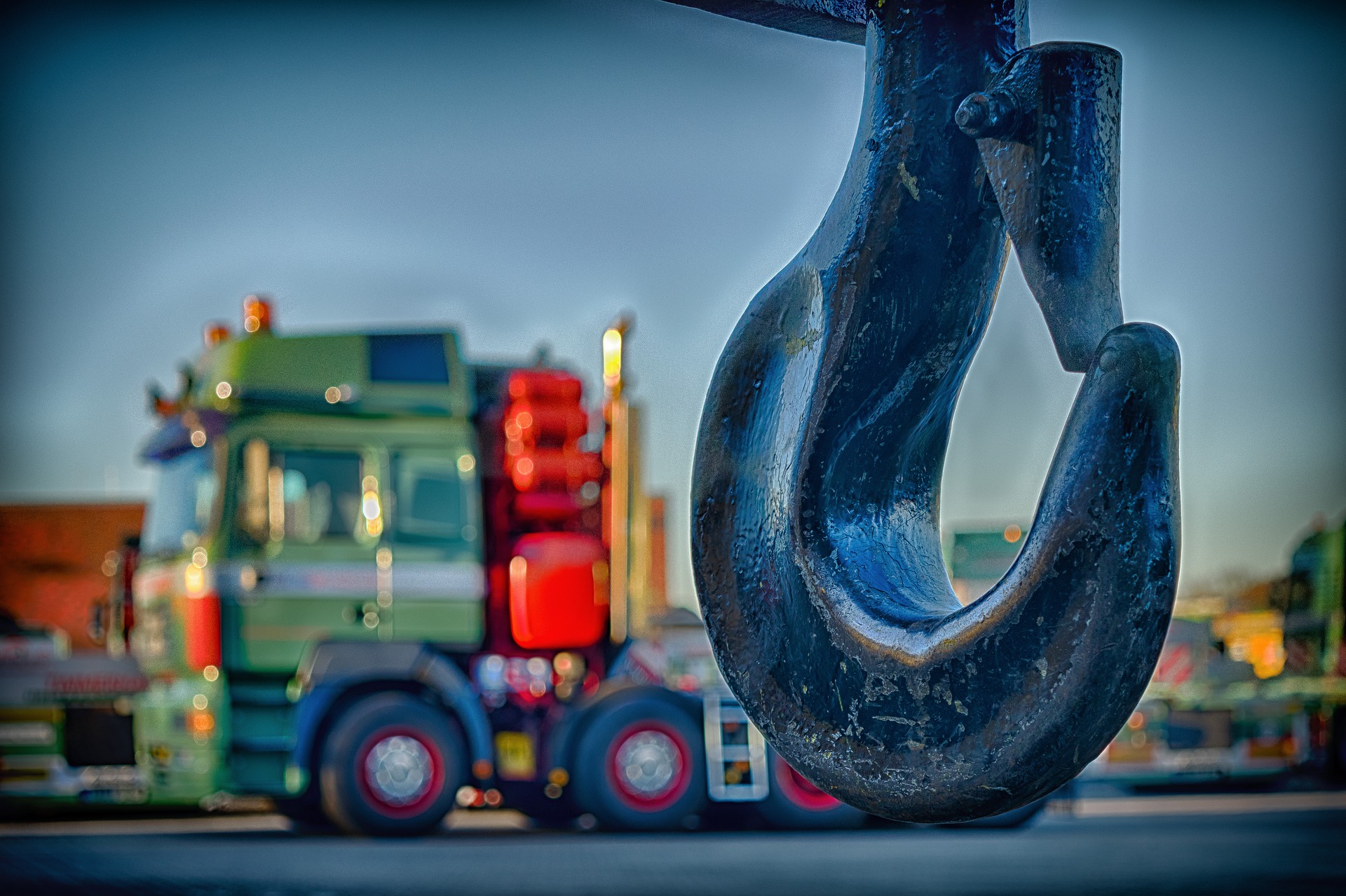
Quais as vantagens de remanufaturar componentes diesel?
30 de junho de 2020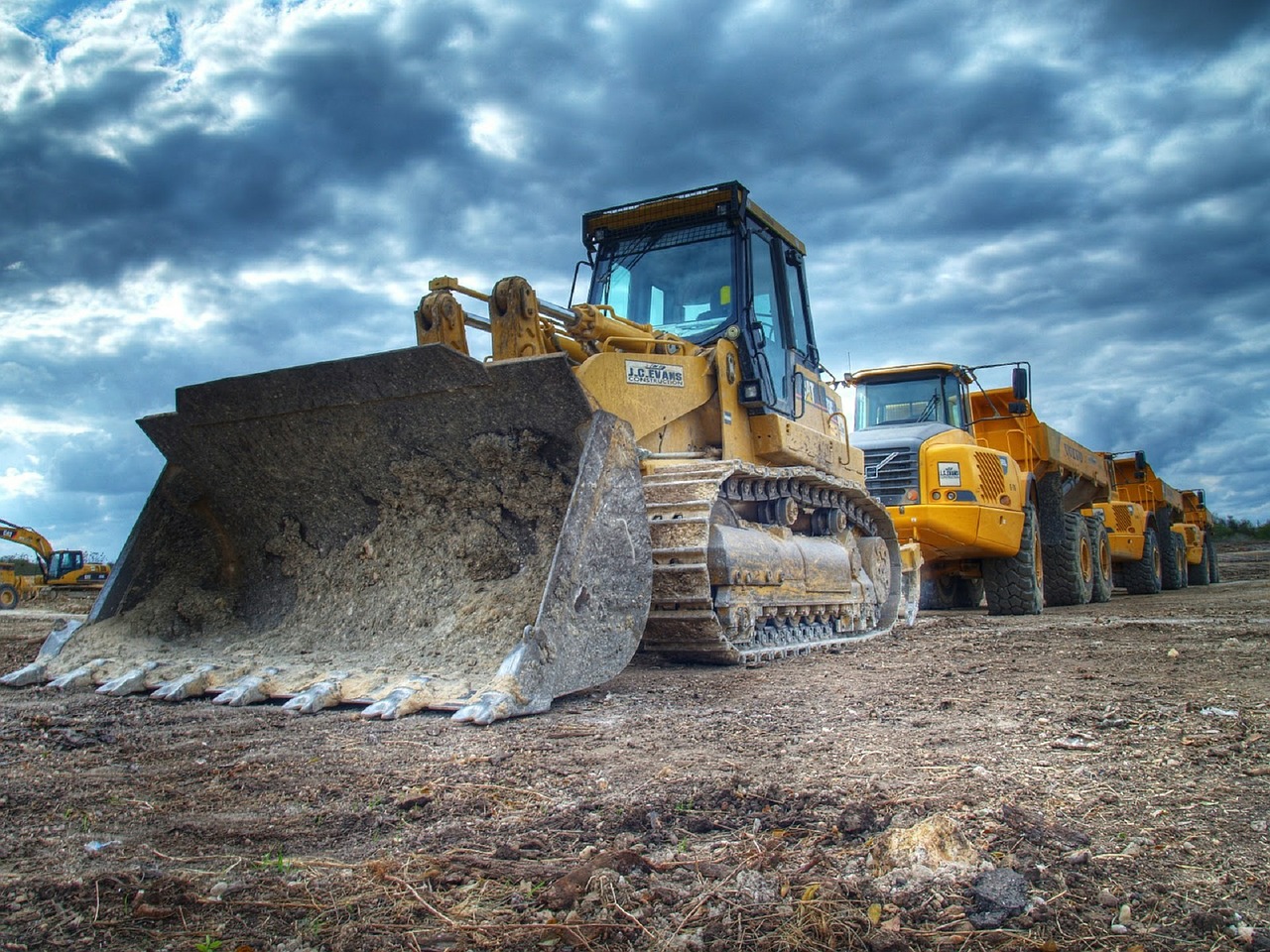
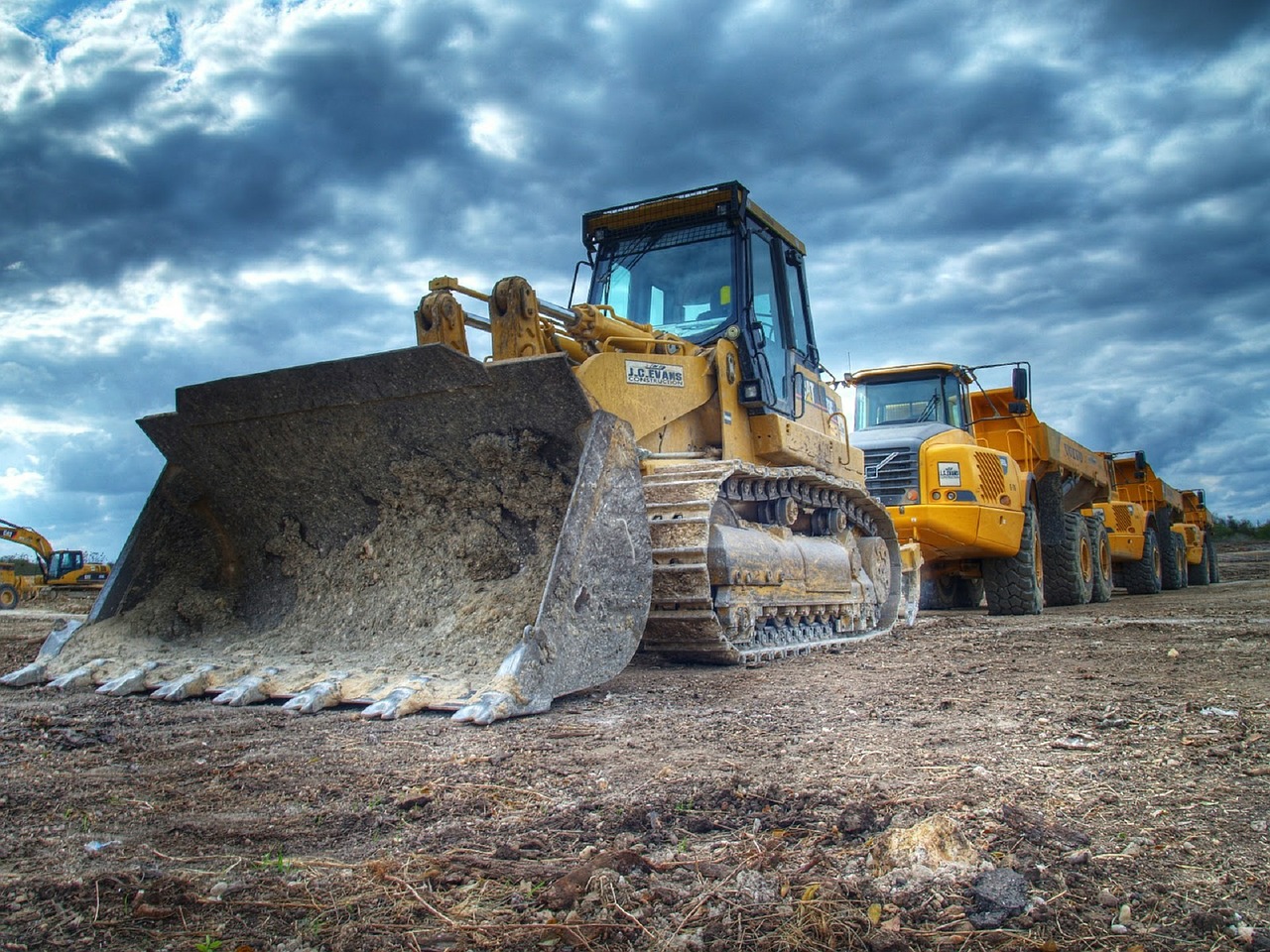
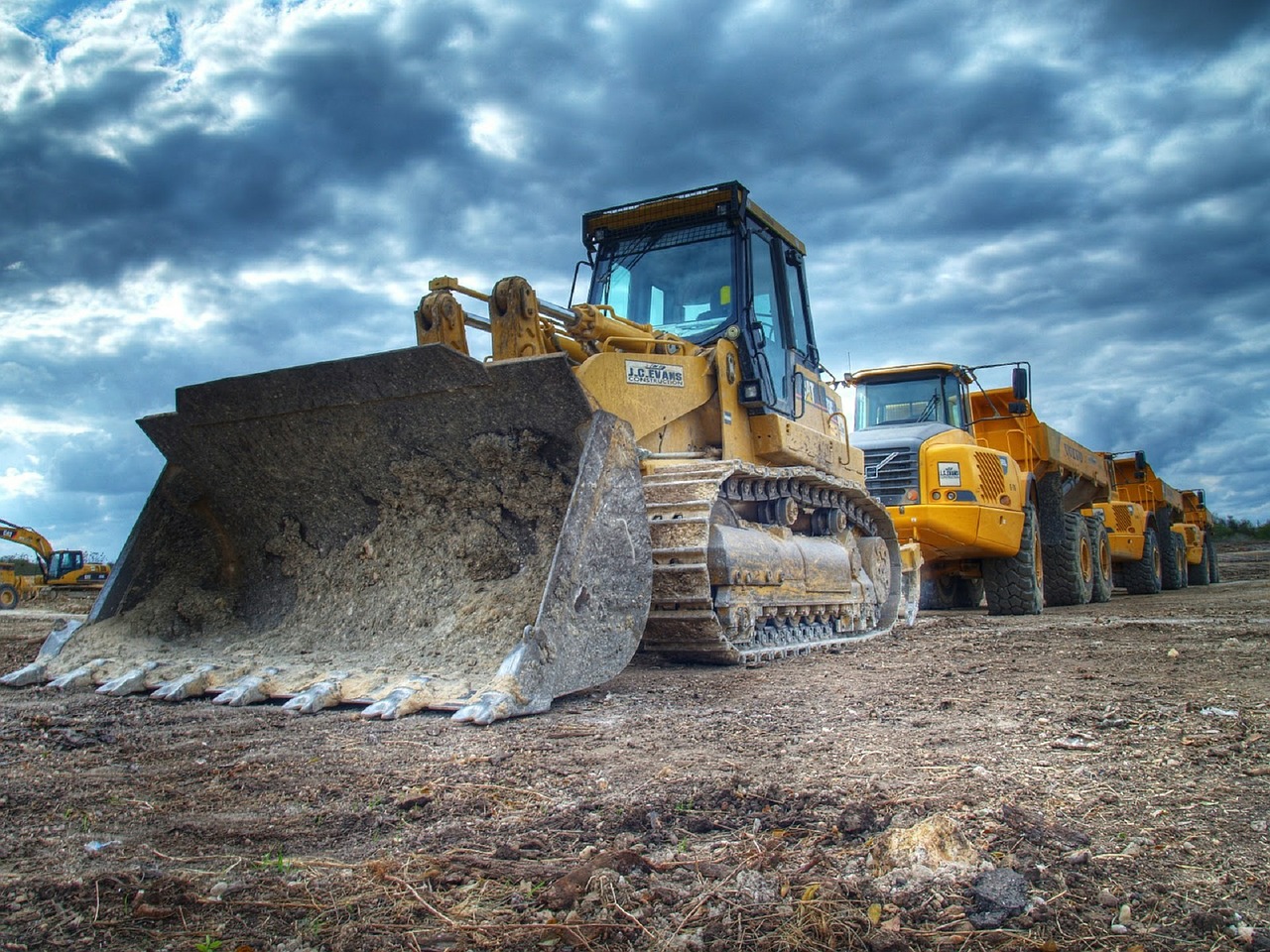
Injetores caterpillar remanufaturados: conheça as vantagens
10 de julho de 2020Qual empresa ou gestor não gostaria de garantir que seu sistema de produção opere da maneira mais eficiente e econômica possível, sem afetar a qualidade do resultado? Pois bem, foi com essa motivação que surgiu o conceito da linha de produção Lean Manufacturing, ou produção enxuta, no bom português.
O Lean Manufacturing é uma filosofia de gestão que consiste em potencializar a produção com a menor quantidade possível de recursos. O conceito surgiu no Japão por volta do ano de 1950, período que sucedeu a Segunda Guerra Mundial. O país enfrentava uma forte crise e não fazia sentido produzir o que fosse em largas escalas.
Um pouco de história
A metodologia da produção Lean Manufacturing nasceu como uma solução para a indústria automobilística Toyota, uma das mais relevantes do setor automotivo mundial. Sakichi Toyoda, pai fundador da Toyota (à época Toyoda Teares), criou o primeiro tear automatizado que, além de fazer as trocas automaticamente, também parava a produção caso algum fio arrebentasse. À capacidade de um equipamento parar e sinalizar alguma falha damos o nome de jidoka, um dos pilares do Sistema Toyota de Produção.
Kiichiro Toyoda, filho de Sakichi, em uma viagem aos Estados Unidos para licenciar a fabricação de teares, entrou em contato com a crescente indústria automobilística da época e se entusiasmou com a possibilidade de levar esse crescimento ao Japão. Voltando ao seu país de origem, Kiichiro iniciou, em 1933, uma linha de fabricação de automóveis dentro da indústria do pai. Três anos mais tarde é lançado o primeiro modelo de veículo, o Satandar Sedan AA 1936, ainda com a marca Toyoda.
Para tornarem a Toyota competitiva e fazer frente às empresas norte-americanas de produção em massa, seria necessário que a Toyota desenvolvesse um novo sistema de produção, adaptável à realidade japonesa, que pudesse atender às necessidades de mercado e às restrições de recursos. Enquanto os ocidentais possuíam linhas de montagem móveis, verticalização, controle de qualidade, administração de estoques e produtos de alto luxo e alto preço, os japonenses criaríam uma cultura diferente, voltada para grupos de trabalho autogerenciados, just-in-time, produção enxuta, círculos de controle de qualidade, produtos de alta qualidade e baixo preço, e melhoramento contínuo.
Em meio a novas ferramentas, métodos e tecnologias, um novo sistema de produção estava sendo criado, prestes a se disseminar ao redor do mundo inteiro e transformar a Toyota em uma das principais indústrias do segmento.
O que é produção Lean Manufacturing
Por meio de uma abordagem sistemática, ocorre um trabalho constante no sentido de identificar e eliminar atividades e materiais que não agregam valor ao processo, quanti ou qualitativamente. Dessa forma, adotaram a prática de produção sob demanda, que contribui para a redução dos estoques e evita desperdícios.
Aumentar a produtividade diminuindo recursos não significa comprometer a qualidade, muito pelo contrário. A alta qualidade dos produtos é prioridade na Indústria Lean, e pode ser garantida por equipamentos que funcionam plenamente e por colaboradores capacitados para solucionar qualquer problema que possa surgir durante a fabricação.
Se você quer aplicar essa metodologia na sua empresa, o primeiro passo é fazer um estudo interno dos possíveis pontos que possam estar prejudicando o desempenho da linha de produção e quais são as dificuldades mais urgentes.
A seguir, vamos apresentar técnicas desenvolvidas no modelo Lean Manufacturing e, a partir da cultura organizacional da sua empresa, você determina quais podem ser mais eficientes neste primeiro momento. Mas, antes de falarmos diretamente sobre as ferramentas, é importante ter em mente as fontes de desperdício mais comuns que podem prejudicar um negócio. São elas:
- Defeitos: erros em peças, materiais, processos e produtos;
- Excesso de produção: aquisição de materiais e produção maior do que a demanda do cliente;
- Estoque: armazenar produtos em grandes estoques, decorrentes do volume excessivo de produção ou da compra desnecessária de matérias-primas.
- Processo desnecessário: relatórios e burocracias que travam a jornada do cliente sem agregar valor algum;
- Movimento desnecessário: deslocamentos que podem ser evitados ou eliminados para conferir mais tempo e eficiência aos colaboradores;
- Transporte desnecessário: tempo perdido com transporte desnecessário de materiais ou com uma logística ineficiente;
- Espera: pausas no trabalho causadas por falhas técnicas, falta de profissionais ou alguma demora entre uma operação e outra.
Para evitar esses desperdícios e conseguir colocar em prática o conceito da linha de produção Lean Manufacturing, algumas técnicas foram desenvolvidas e são essenciais para alcançar os resultados completos de redução de custos e aumento da produtividade.
- Mapeamento do fluxo de valor: ferramenta criada para implementar o processo de melhoria contínua de forma mais sistêmica dentro de toda a cadeia produtiva da indústria. Depois de identificar os problemas que bloqueiam a eficiência da produção, é criado um fluxo que traz soluções. Resumindo: observe como funciona a linha de produção atual e qual seria o caminho ideal para gerar melhores resultados.
- Métricas Lean: indicadores que você deve acompanhar para medir o desempenho do seu negócio. Algumas dessas métricas são: o lead time (tempo que o produto leva entre o início da produção até ser entregue ao cliente); o cycle time (tempo utilizado para realizar um processo); e a throughput (quantas unidades são produzidas em determinado período).
É recomendável definir um time de profissionais que se dedique à análise desses dados, para convertê-los em soluções reais e não apenas serem armazenados.
- Kaizen: esse conceito tem como centro a crença de que sempre podemos aprimorar nosso trabalho, tornando-o mais inteligente dia a dia. Para desenvolver o comportamento Kaizen, existem 9 práticas que devem ser adotadas em sua rotina profissional e pessoal.
- Padronização: esse conceito está presente em toda a filosofia Lean. Os padrões são usados para alcançar um aperfeiçoamento contínuo, outra peça-chave nesse tipo de produção. Assim, mantém-se a qualidade e estabilidade dos processos.
- TPM (Total Productive Maintenance): um conjunto de ações para prever e eliminar possíveis falhas nos equipamentos da indústria, a partir de manutenções preventivas e revisões periódicas planejadas.
A Turbo Brasil, empresa com 20 anos de mercado que realiza o comércio e a remanufatura de turbinas, sistemas de injeção e outros componentes de motores diesel, trabalha com a metodologia da produção enxuta, garantindo sustentabilidade e qualidade de serviços. A empresa, que tem sede em Contagem-MG, trabalha investindo constantemente em novas tecnologias para aperfeiçoar seus processos e garantir a tradição de ser referência em toda a América Latina.
As técnicas que citamos são apenas algumas das técnicas fundamentais da produção Lean Manufacturing para serem colocadas em prática no seu negócio. Lembre-se que é essencial respeitar suas particularidades e entender o momento certo de aplicar cada uma delas.
Agora que você já sabe o que é e como se desenvolveu o conceito de produção Lean Manufacturing, que tal entender como evitar falhas prematuras dos componentes de motores diesel?